Don't Ignore the ATG
Written by: Brian Pottebaum, Director of Training Services
ATG is short for Automatic Tank Gauge which is an electronic device that can be used to monitor petroleum storage tanks. The ATG functions as an important fuel management tool and can be found at most petroleum storage tank facilities.
ATGs can be used for many functions that include fuel inventory management, water detection, as well as leak detection on the tanks and lines. They are designed to alert the operator by indicating alarms and warnings when the system detects a problem. ATGs have evolved over time and have become more accurate and diverse. They can be checked locally and remotely by facility personnel. Most of the newer models can store significant testing and system status documentation to aid the operator in regulatory compliance.
ATG “systems” include the ATG (monitor or console) and the inventory probe that is placed in the corresponding storage tank or tanks. Occasionally the system will include an overfill alarm box that is installed outside by the tank filling area. That is programmed through the ATG to alert the fuel delivery person when the tank has reached 90% full.
The inventory probe electronically monitors the product level and relays that information back to the ATG. The probe extends from top to bottom of the tank and has two calibrated floats mounted on the shaft. There is one float calibrated for the fuel being stored in the tank, and there is also a second float that is calibrated for water.
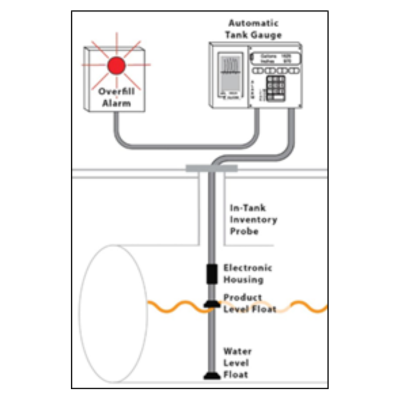
Fuel Inventory Management
One of the main functions of the ATG system is to manage fuel inventory. Diligent fuel managers track the fuel in their system to account for all gallons being deposited and gallons being sold, also known as throughput. Keeping track of how much fuel you have available is important and helps determine when to order more fuel. It can also help determine if any gallons are missing. Temperature must also be monitored by the ATG because temperature changes cause expansion and contraction of the petroleum molecules, which will directly affect the product level in the tank.
The ATG should be checked daily to make sure the tank system is operating properly. To maintain compliance with the state and federal 30-day walkthrough requirements, you must check the ATG every month (at a minimum) and record your findings on the appropriate form. Each state has their own form that should be used to document that the tank has passed a 0.2 gph leak test within the last 30 days, as well as any alarms have been cleared (and any issues corrected).
Water Detection
As part of the fuel inventory management, make sure to check the tanks for water along with the fuel levels. Accumulated water will throw off the fuel level and will eventually cause fuel quality issues. Water inside the tank becomes the perfect environment for bacteria to thrive, which will lead to additional expenses to treat and eliminate the pests.
Water is also a very good conductor that will produce a corrosive environment inside the tank. Metallic components inside the tank, as well as the steel tank, will quickly show signs of corrosion.
In the age of renewable fuels, specifically ethanol blends, it is extremely important to check for water in petroleum storage tanks. Water that is allowed to accumulate will eventually bond with the ethanol in the fuel and cause a phenomenon called phase separation. This happens when the moisture or water saturation increases in the fuel, eventually causing the ethanol that has absorbed the water to separate from the gasoline or fuel and sink toward the bottom of the tank. The phase separation layer that has formed on the bottom of the tank, which could be several inches deep, can also go undetected if you are not properly equipped to check for it. Specific probes, filters, and water finding pastes must be used to detect this solution. Phase separation that is dispensed into vehicles will cause extensive damage.
Leak Detection
Another key function of the ATG is the ability to monitor the fuel system for leaks. This can be done several different ways using probes, sensors, transducers, and algorithms. Depending on the components and software that make up your ATG system, you must retrieve a specific report or printout every 30 days at a minimum. You must also continuously maintain 12 months of the “30-day leak detection printouts” to comply with regulatory requirements. For example, if the records are requested by the regulator on June 1, 2024, you will need to produce adequate monthly leak detection records that go all the way back to May 2023.
ATG systems that are routinely conducting 0.2 gph leak tests will typically print a report every time a test is completed. This may result in many printouts, but you are only required to keep one passing test per tank per month. Make sure to file the fullest possible passing test for each tank every 30 days. Obviously, if there is a failed leak test, you will need to address it immediately - clear the alarm and run another test to make sure the tank is not actually leaking. Your service provider may need to help troubleshoot the issue, as it may be faulty equipment or programming. If the leak alarm continues, don’t forget to contact the state regulators within 24 hours to report the suspected petroleum release.
If you have pressurized delivery from tank to the dispensers and have electronic line leak detection (ELLD) as part of the ATG system, you should have the ability to retrieve leak test reports for the lines from the ATG. Make sure to review these test results as you do tank testing. Most ELLD systems can run 3.0 gph, 0.2 gph, and 0.1 gph line tightness tests, and will attempt to cycle through each test every time the pump turns on/off. However, if not given enough time in-between dispensing transactions, it may not complete all three tests and not record the results. The 3.0 gph line test is a very quick test and it is unusual to find no 3.0 gph passing test results in the last 24 hours, unless it is a fueling facility or low throughput product where the pump does not cycle on/off routinely. Failed line tests will be indicated in the same way as failed tank leak tests. These alarms must not be ignored and need to be reported to the regulators within 24 hours if a release has occurred.
ATG systems that are equipped with liquid sensors in the double wall (interstitial) tanks and/or piping system typically print a report every time a sensor detects liquid. However, as part of the regulatory requirements, you need to document every 30 days that the system is not in alarm, so you will need to retrieve a sensor status report that indicates that the system is in normal status. This may require some maintenance to correct the issue to return the sensor to normal status. Quite often liquid has accumulated and must be removed from a specific containment area so the sensor can reset.
Alarms
The most overlooked feature of the ATG system is the ability to detect and display alarms. There is a long list of alarms that can occur on the ATG and the severity ranges from simple warning to very serious issue. Multiple active alarms can exist at the same time and may be related to the same problem, or they can be related to completely different issues. Take the time to sort through the alarms and address them appropriately. Because ATG alarms are common, operators tend to get complacent and ignore them. This is poor management and can lead to very expensive environmental cleanup if the practice continues.
Some ATGs require each alarm to be manually cleared and some will clear by themselves once the situation has been corrected. System alarms are typically indicated by visual lights, audible noise, and printouts. All alarms must be addressed immediately; Never ignore alarms.
As was mentioned earlier, checking for alarms is required as part of the 30-day walkthrough inspection. Even though documentation is only required every 30 days, best management practices suggest that the ATG is checked every day and all alarms are addressed immediately. Issues that get resolved sooner, have a better chance for less environmental impact.