Fuel Inventory Management- Don't Lose Track of Your Fuel
Written by: Brian Pottebaum, Director of Training Services
How closely do you watch your fuel inventory? Do you manage the throughput to make sure no fuel is missing? Daily product inventory control is a process that can be used to manage fuel throughput, in addition to monitoring for leaks from the tanks and associated piping.
This process involves a comparison of the physical “stick” inventory to the book inventory. In other words, you will measure and calculate the amount of product you should have in the tank after you take your starting inventory, add any deliveries, and subtract the amount of product pumped. A general comparison could be made to a checkbook ledger, where you balance your bank account with deposits and withdrawals for each month to make sure every dollar is accounted for.
Besides product leak detection, daily inventory control has many other management benefits, such as finding water intrusion, delivery verification, and dispenser meter accuracy. Inventory control reflects what is going on with the fuel in your storage system between the fill cap and the dispenser meter. But the reliability of this information is only as good as the care you take in carrying out the inventory-control procedures.
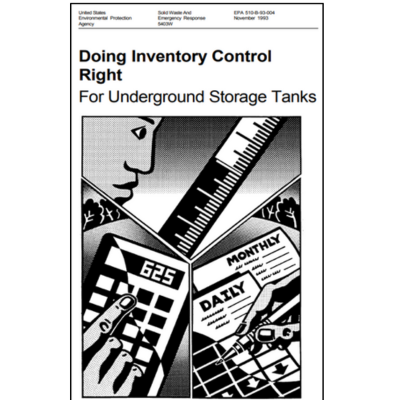
The EPA developed a guidance document for conducting inventory control (in November of 1993) and at that time was a temporary means to meet federal requirements for leak detection on the underground storage tank systems. Most states no longer accept this practice as a stand-alone method of leak detection; however, the practice is still encouraged to strengthen fuel inventory management at each facility. The complete document can be located here https://www.epa.gov/sites/default/files/2014-03/documents/inventry.pdf
Fuel inventory management involves three essential steps:
- Take daily measurements of fuel in the tank, fuel delivered, and fuel dispensed.
- Reconcile the daily measurements to determine the daily variance.
- Calculate the monthly variance to determine whether your monthly variance is within regulatory guidelines.
Taking Daily Measurements
The process must be consistent and conducted every day that the system has fuel added or removed. Product levels can be measured physically with a gauge stick or taken from an electronic tank level monitor, usually referred to as an automatic tank gauge (ATG). Readings should be recorded on the daily inventory worksheet, along with totalizer readings (total gallons pumped) and any fuel delivered to the tank. Don’t forget to check for water and record it. This may require the use of water finding paste that is spread on the bottom portion of the tank gauge stick. The paste will change colors if it comes into contact with water.
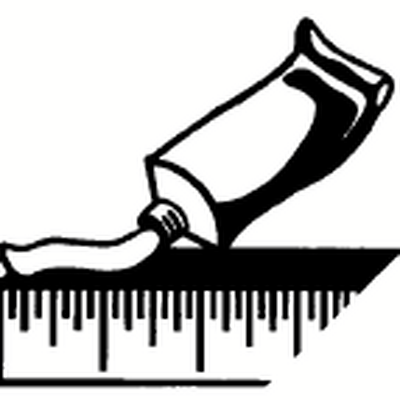
When using a tank gauge stick, make sure it is readable to the nearest 1/8th inch all the way to the bottom and the button is still on the bottom of the stick. You will also need the appropriate tank chart so the inches measured can be converted to gallons for the report. Tank sticking should be done carefully through the fill pipe that includes a drop tube that extends to near the tank bottom. Let the stick gently touch the bottom, then quickly bring it back up. Read the depth of fuel indicated by the wet mark to the closest 1/8 inch division on the stick.
In addition to the regular sticking that is done at the same time every day for inventory records, you should also take stick readings before and after every delivery. This is a good way to check the amount of fuel that was actually delivered.
You also need to know how much fuel has been removed from your tanks daily. Your point of sale (POS) will have the total amounts of fuel that have been pumped by product, otherwise some dispensers have “totalizer” meters on them that track the amount of fuel that has been pumped through each meter. The totalizers would need to be added together so you can obtain the total amount of that product that has been pumped for the day.
Important: Regardless of how you gather the total amount of fuel pumped, make sure to keep the process consistent from day to day and that no fuel is added or removed between the stick reading in the tank and the totalizer readings.
Reconcile Daily Measurements
This part of the process requires you to copy information from the daily inventory worksheets to the monthly inventory worksheet for each month. After copying the information over, you will need to do some math, or set up an electronic spreadsheet that will do the calculations automatically.
As the “SAMPLE Monthly Inventory Record” image shows, you will be calculating the daily book readings (gallons) by adding any gallons delivered and subtracting the gallons pumped for each day. You also need to have the stick reading conversions recorded so you can compare the daily over/short.
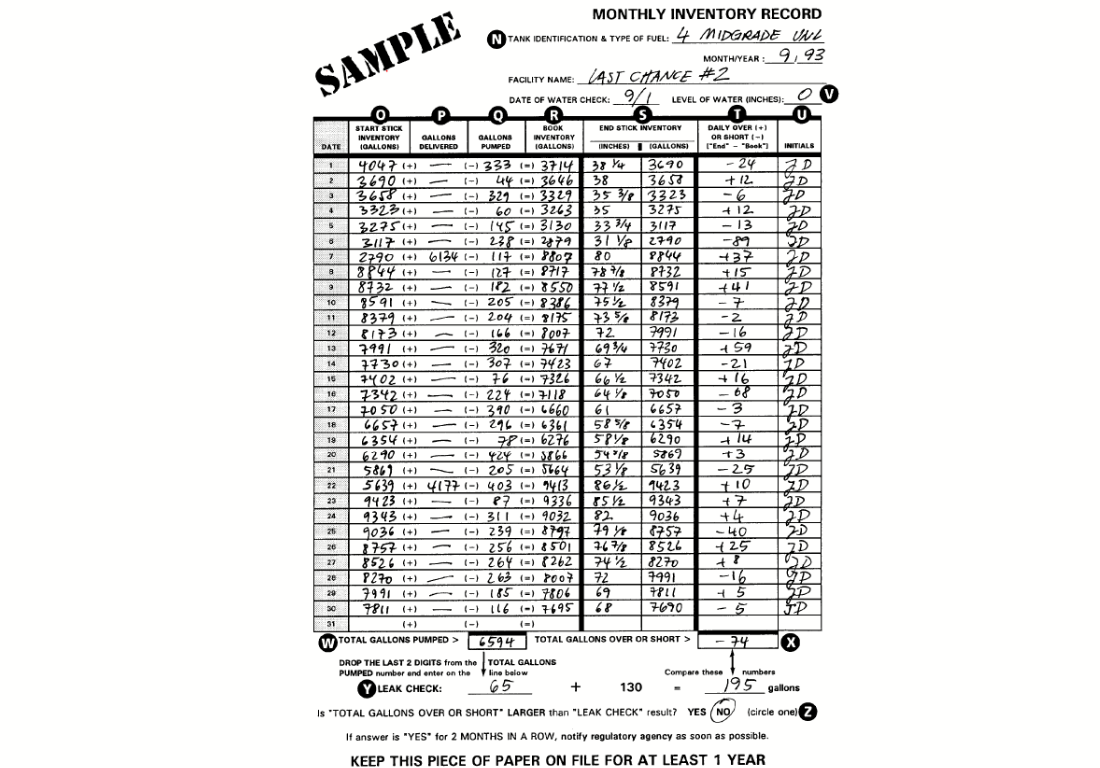
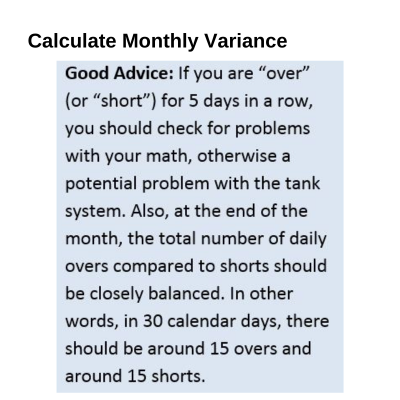
At the conclusion of each month, you will need to compare the “stick” inventory and the “book” inventory to determine if the data is indicating excessive fuel loss or gain. To do this you will need to add up all the gallons pumped. To determine if the system is within the leak tolerance, multiply the total gallons pumped by 1% and add 130 to get your leak check value. Then you will add up the daily over/short column to get the total (+/-) for the month, paying careful attention to positive and negative numbers to get an accurate total. By comparing this total over/short value to the leak check value that you calculated, you can determine if your monthly inventory is within the allowable variance.
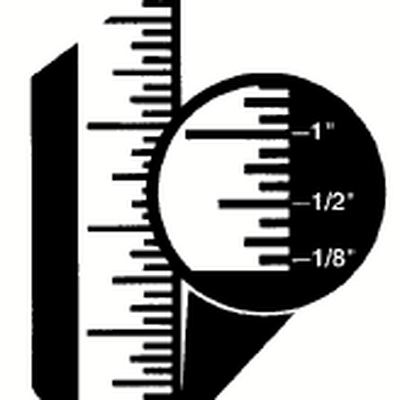
Common Problems or Errors
The primary purpose of daily inventory control is to provide for a frequent check of what you think you have in inventory versus what you actually have in the tank. If these numbers are not in agreement, it might mean you measured incorrectly, misread your gauge stick, or made an error in your math. Here is a list of some other common mistakes that lead to problems with the process.
- Measurement Errors. Inventory must be measured carefully and recorded accurately. Different staff may take the measurement differently or read the measures differently. Avoid it by training a staff member and have the same person take the measurements each day.
- Petroleum Creep. This occurs when your gauge stick absorbs petroleum and wicks it upwards, giving you a false reading. Avoid it by taking readings quickly and using a gauge stick that is properly sealed with clear coat.
- Tank Pressure or Vacuum. Tanks with vapor recovery systems may have pressure or vacuum differences within tanks that can affect stick readings (in the fill pipe) and ATG measurements. Avoid it by adding a pressure relief valve into the vapor system, or manually relieving pressure or vacuum prior to taking measurements.
- Equipment Error. ATGs and totalizers can lose their accuracy over time. Avoid it by calibrating (adjusting) them regularly. Check equipment owners’ manual or equipment supplier on how to do calibration for the specific system. Totalizers/meters should be calibrated annually. You should also compare your totalizer readings to your sales terminal readings to ensure sales have not been missed.
- Delivery Error. The amount ordered may not be the amount delivered. If you have more than one tank for a product, the delivery may be credited to the wrong tank, or a delivery may be split over two tanks but counted as one delivery. Tanks can be overfilled. Avoid it by measuring before and after deliveries. This reduces the chances of overfill and confirms the amount of inventory delivered matches the invoice/delivery receipt and is credited to the proper tanks. Wait at least five minutes after product is delivered before measuring to let it come to temperature.
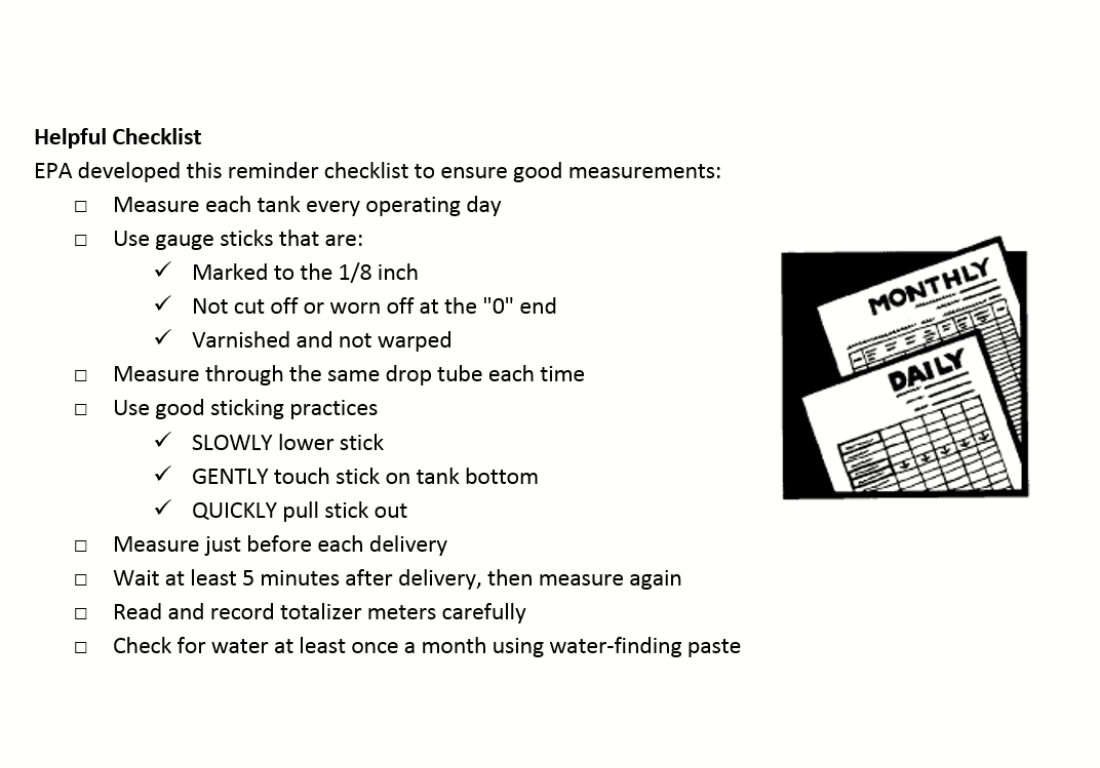