Testing Your Line Leak Detector
Written by: Brian Pottebaum, Director of Training Services
At fueling facilities, customers expect to get in and out fast. To meet this demand, more dispensers and pressurized fuel delivery systems are installed. Unfortunately, this increased demand for convenience brings the increased risk for system failures and serious piping leaks, so the systems must be constantly monitored.
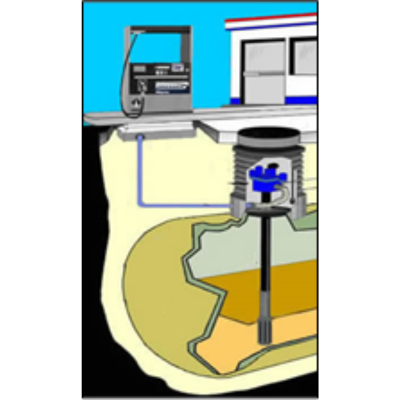
Pressurized Delivery System
A pressurized fuel delivery system will have a submersible turbine pump (STP) installed at the tank that will push the product to one or multiple dispensers. Each tank/product will have a separate delivery system with a dedicated STP, except for blended products at the dispenser.
Pressurized fuel delivery systems are required to have some form of automatic line leak detection (ALLD), which must be used in conjunction with periodic line tightness testing. ALLD is intended to detect a “catastrophic” loss or a line leak that exceeds 3.0 gallons per hour (gph) at 10 pounds per square inch line pressure within 1 hour. All pressurized lines must be equipped with this, and state and federal regulation require that they be tested annually in accordance with the manufacturer’s specifications. Each manufacturer may have their own specific procedures to adequately test the leak detector for proper operation, otherwise a recognized standard or code of practice should be used to meet the requirement. Pressurized lines must never operate without some form of automatic line leak detection.
According to state and federal regulation, ALLD must recognize a line leak that exceeds 3 gph and alert the fuel system operator by restricting flow through the line, shutting down the product line, or going into leak alarm (requiring the operator to respond accordingly). Acceptable methods of ALLD include mechanical line leak detection (MLLD), electronic line leak detection (ELLD), and in some cases electronic sump sensors.
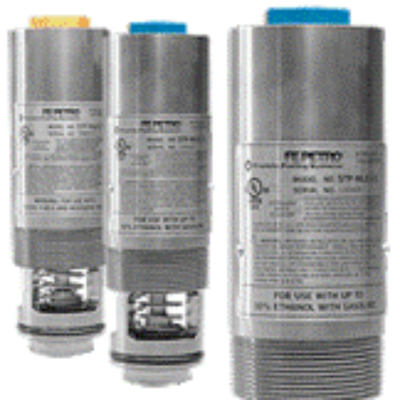
Mechanical Line Leak Detection
MLLD will only accomplish 3.0 gph leak detection. That is why an annual line tightness testing at 0.1 gph or monthly monitoring is required on the pressurized lines in addition to the annual MLLD functionality test. The submersible pump must cycle on/off to actuate the MLLD and test for leaks prior to dispensing fuel through the dispenser. The customer can expect a normal flow through the nozzle to be around 7-8 gallons per minute.
In the event of a line leak exceeding 3 gph, the MLLD will restrict flow (or slow flow) and allow only 1 to 3 gallons per minute through the dispenser. This will usually prompt the customers to complain about the dispenser pumping so slowly, at which time you should contact your service company and make any necessary repairs.
There are several incidents that can trip the MLLD, even though there isn’t a leak, such as a malfunctioning check valve, thermal contraction, and air in the lines. If the leak detector is operating properly and not in slow flow, but you are still not getting adequate flow through the dispenser, it is possible that the fuel filter is plugged and needs to be changed. There are also several instances that can cause MLLDs to miss leaks, such as continuously running submersible pumps, piping with excessive head pressure, malfunctioning MLLDs that trip above 3 gph, and satellite dispensers with improperly placed solenoid valves.
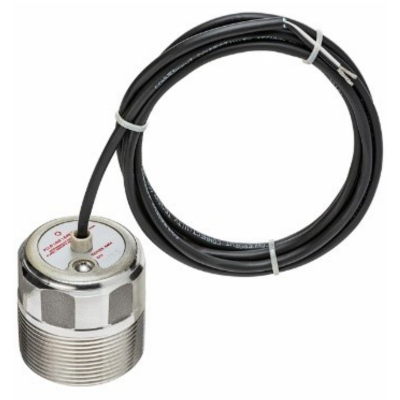
Electronic Line Leak Detection
ELLD is usually wired through the automatic tank monitor, but some do offer stand-alone monitoring. Most ELLDs have the capability to run 3.0 gph, 0.2 gph, and 0.1 gph line tightness testing. Also, some of the newer software offers continuous leak detection, which will run all three tests daily if given enough idle time between dispensing. Like the MLLD, it requires the submersible pump to cycle on/off to start the line testing process. However, the testing generally takes place after the pump has cycled off and the nozzle is no longer dispensing fuel.
In the event of a leak or unusual operating conditions, the ELLD will alarm and shut the system down. In most cases, you will have to contact the service company to make necessary repairs and reset the system. Obviously, these monitors can be programmed to test however you want, but it is recommended that you use every function the ELLD offers, which would include all three levels of testing.
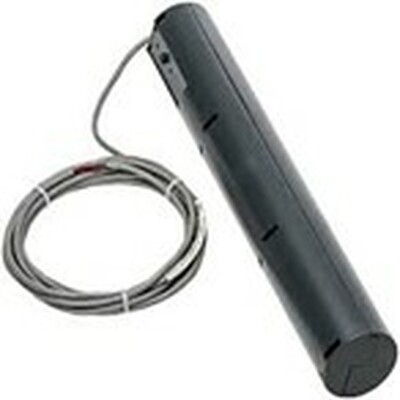
Electronic Sump (Liquid) Sensors
Although not a favorable method without additional line leak detection equipment, electronic sump (liquid) sensors can be a form of catastrophic line leak detection in some installations, such as emergency backup generator systems and tanks used to supply fuel to emergency response vehicles. To accomplish this, they must be wired for positive shutdown once the sensor goes into alarm status.
Multiple sensors are placed in contained sump areas and positioned properly at the bottom of the containment. Leaks must be detected immediately once the containment starts to collect leaked product. Water infiltration, sump deterioration, and sensor failure keep this from being a reliable method.
Testing the ALLD
If the ALLD is not installed and tested properly, how would you know that it will alarm, shut the system down, or restricting flow at 3.0 gph leak rate? Testing the ALLD properly requires certified and calibrated equipment that will indicate whether the leak detector is “seeing” a leak at 3.0 gph. In addition to adequate testing equipment, the leak detectors must be tested by a qualified technician.
As stated earlier, the leak detector must detect a leak exceeding 3.0 gph but has limitations and anything less than that may go undetected, so any slow seeps or drips will not trip the leak detector. Also, the leak detector does not monitor most of the dispensing unit because it is isolated by a solenoid. This is one more reason to routinely look inside your dispensers and sumps.